Fermer
Carreaux céramiques : Types, caractéristiques et classification
CARREAUX CERAMIQUES : DÉFINITION ET CARACTÉRISTIQUES
Les carreaux céramiques sont des matériaux de construction qui ont depuis toujours été utilisés pour habiller les sols et les murs des habitations. Ils sont obtenus par le mélange d'argile, de feldspath, de kaolin, de quartz, d'additifs chimiques et d'eau en différentes quantités et proportions, séchés et cuits à très haute température (entre 900 °C et 1 250 °C). Les carreaux sont habituellement utilisés pour des pièces telles que la salle de bains ou la cuisine.La matière première de base pour la production de céramiques est l'argile, dont la caractéristique fondamentale est sa plasticité : trempée dans l'eau, elle peut être façonnée en différentes formes qui se maintiennent après séchage.
Il existe différents types d'argiles, qui diffèrent par leur teneur en sable, et qui donnent une couleur et une porosité spécifiques.
L'argile utilisée pour la production peut être de 2 types :
- Argile blanche : provenant d'Europe du Nord, elle est généralement plus précieuse et donc plus chère ;
- Argile rouge : provenant d'Italie et d'Espagne, plus courante et donc moins chère.
Le corps du carreau lui-même est appelé support et, dans le cas des carreaux émaillés, il est recouvert d'un vernis généralement coloré.
Le mélange qui compose les carreaux peut prendre sa forme finale par deux processus différents :
- Pressage: les matières premières en poudres sont compactées au moyen de presses à haute pression : on obtient ainsi des carreaux en grès cérame, monocuisson et bicuisson ;
- Extrusion: la forme finale est obtenue en faisant passer le mélange ramolli par des orifices spéciaux : on obtient ainsi de la terre cuite et du klinker.
Le support peut être poreux ou compact : ces caractéristiques ne peuvent pas être évaluées à l'œil nu, mais il est important de savoir qu'un support compact sera plus résistant à l'absorption de l'eau et plus résistant aux chocs.
En fonction des matières premières utilisées dans le mélange, le support peut prendre une grande variété de couleurs : pâte rouge, pâte blanche, colorée.
Une fois le support réalisé, le carreau peut avoir une surface émaillée ou non.
Les carreaux émaillés ont le support recouvert d'une fine couche de matériau vitreux ; il existe des émaux de tous types et les effets esthétiques qu'ils donnent aux carreaux sont les plus variés.
Les carreaux non émaillés ne présentent pas de différence entre la surface et le support. Ils peuvent subir des traitements spéciaux qui modifient leur aspect, comme le polissage et le semi-polissage.
Les carreaux peuvent être de différentes formes, les plus populaires étant les carreaux carrés et rectangulaires, et diffèrent par ailleurs en termes d'épaisseur, allant d'un minimum de 3,5 à un maximum de plus de 20 millimètres, avec une valeur moyenne variant de 7 à 10 mm.



Cette grande variabilité des formats offre d'infinies possibilités créatives pour la réalisation d'espaces toujours plus élégants et modernes : ces dernières années, l'architecture s'est beaucoup concentrée sur les environnements créés avec des formats moyens et grands tels que 20x120, 30x60 et 60x60.
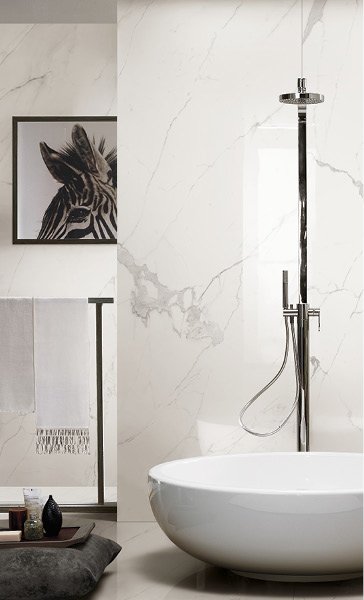


CLASSIFICATION NORMATIVE DES CARREAUX CÉRAMIQUES
La classification des carreaux céramiques est strictement réglementée par la norme EN14411, qui identifie 9 groupes en fonction de 2 paramètres : la méthode de formage et l'absorption d'eau.Deux méthodes de formage sont envisagées : l'extrusion et le pressage.
- Pour l'extrusion (utilisée pour des produits tels que la terre cuite et le klinker), le mélange de matières premières est préparé sous la forme d'une pâte dont la teneur en humidité varie, selon le type de produit, entre 15 et 20 %. On force ensuite la pâte à passer à travers une ouverture qui reproduit la section transversale de la tuile. Une bande continue du mélange sort alors de cette ouverture, qui est ensuite coupée selon le format souhaité.
- Pour le pressage (la technique la plus utilisée en Italie, pour des produits tels que le grès cérame, les carreaux monocuisson et bicuisson), la pâte est préparée sous forme de poudre avec un taux d'humidité d'environ 5 %. Cette poudre est comprimée dans un moule qui reproduit la forme du carreau.
L'absorption d'eau est une mesure de la quantité d'eau que le carreau peut absorber dans certaines conditions. Étant donné que l'absorption se produit à travers les pores du matériau, qui sont en communication avec la surface externe, l'absorption d'eau constitue une mesure de la quantité de pores, qu’on appelle « porosité ouverte » (la « porosité fermée », au contraire, est formée par les pores qui ne sont pas en communication, et donc non accessibles depuis la surface externe).
L'absorption d'eau fournit donc une indication immédiate de la structure du matériau :
- une absorption d'eau élevée : structure poreuse ;
- faible absorption d'eau : structure non poreuse ou compacte (présence de grès).
Ces deux variables donnent lieu à la classification suivante :
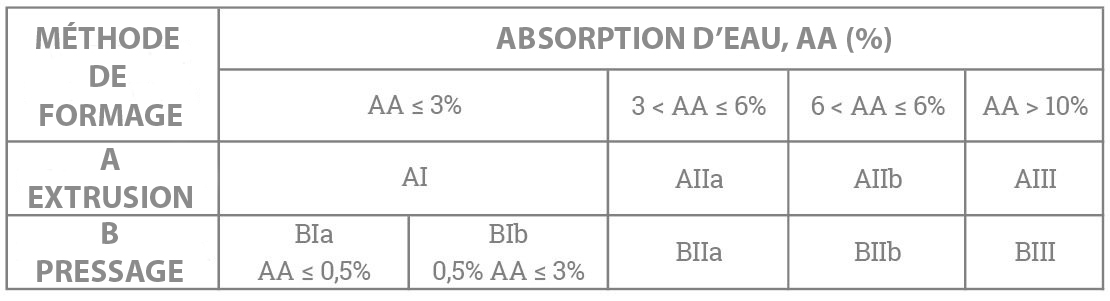
GRÈS CÉRAME, MONOCUISSON ET BICUISSON
Grès cérame, monocuisson et bicuisson sont les noms sous lesquels sont connus les carreaux produits par pressage :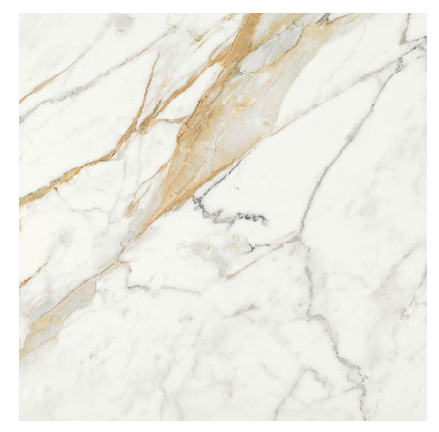

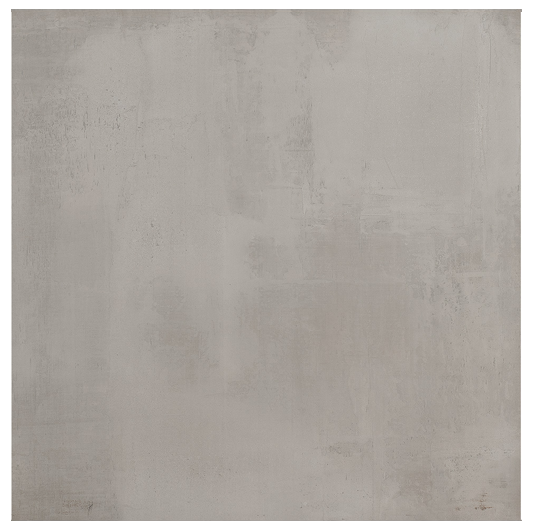
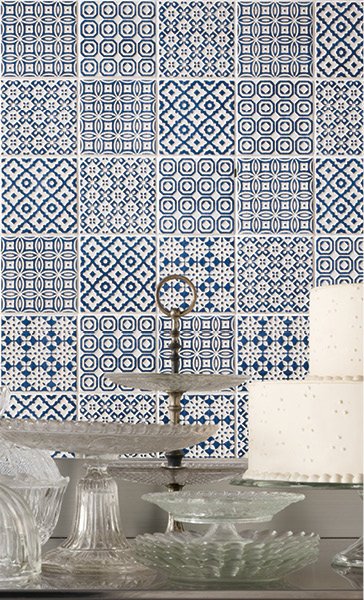


- grès cérame (classe BIa, absorption d'eau entre 0 et 0,5 %) : il s'agit d'un carreau cuit à une température allant d'un minimum de 1 180 °C à un maximum de 1 250 °C, dans lequel la haute température de cuisson et l'argile sélectionnée confèrent au produit final une grande résistance et une absorption d'eau pratiquement nulle. Parmi ses principales caractéristiques figurent : la dureté, la résistance au gel, la résistance aux agents chimiques et l'imperméabilité. En raison de ses performances et de ses caractéristiques, techniques mais aussi esthétiques, il convient aussi bien à des solutions de revêtement intérieur qu’extérieur, allant des bâtiments publics aux habitations privées. Aujourd'hui, le grès cérame est le type de matériau céramique le plus avancé et couvre environ 80 % de la production italienne ;
- monocuisson (classes BIb-BIIa-BIIb, absorption d'eau supérieure à 0,5 % et inférieure à 10 %) : carreaux obtenus par la cuisson simultanée du support céramique et de l'émail à une température comprise entre 1 050 °C et 1 180 °C. Ces carreaux ont une porosité plus élevée que le grès et ont donc une structure plus faible mais sont plus faciles à percer. C'est pourquoi ils ne conviennent que pour être posés en intérieur ou éventuellement sur les murs. Ils peuvent être à pâte rouge (pâte de moindre valeur que l'on trouve principalement dans le sud de l'Europe, caractérisée par une forte présence de fer) ou de pâte blanche (pâte de plus grande valeur que l'on trouve principalement dans le nord de l'Europe) ;
- Bicuisson ou faïence (classe BIII, absorption d'eau supérieure à 10 %) : Les carreaux bicuisson sont fabriqués en cuisant le biscuit brut une première fois, puis une seconde fois après émaillage, à une température allant de 900 °C à 1 050 °C comme température maximale.
Par rapport aux carreaux monocuisson, ceux-ci ont une absorption encore plus élevée, ce qui les rend plus délicats, et donc adaptés aux murs intérieurs seulement, et non aux sols.
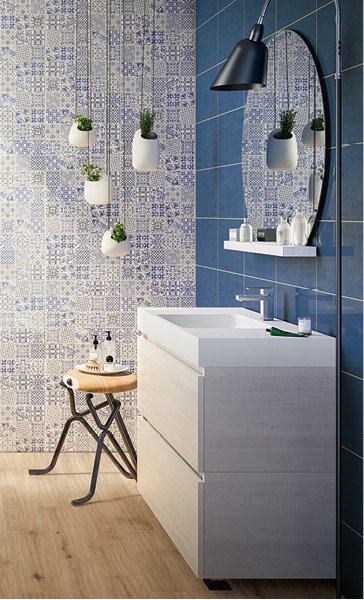
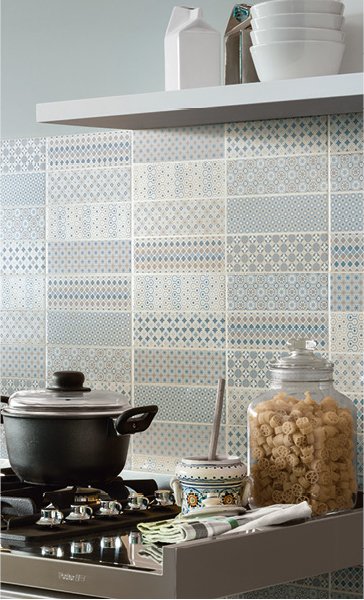

CARACTÉRISTIQUES TECHNIQUES ET ESTHÉTIQUES
En plus des caractéristiques réglementées par la norme EN 14411, il existe toute une série de caractéristiques qui définissent davantage les carreaux céramiques d'un point de vue esthétique et commercial. En fonction de l'espace dans lequel ils seront utilisés, il est possible de trouver le bon modèle sur IPERCERAMICA, qu'il s'agisse de carreaux de cuisine ou de carreaux de salle de bains.Les carreaux peuvent être émaillés, lorsque la surface est recouverte d'une couche de verre colorée, dont l'épaisseur varie de quelques dixièmes de millimètres à 1-2 millimètres, et qui leur confère des caractéristiques esthétiques (couleur, brillance, décoration, nuance...) et techniques (dureté, imperméabilité...).
Les carreaux émaillés peuvent ne pas être teintés dans la masse lorsque la couleur de la pâte intérieure est différente de celle du vernis superficiel, ou teintés dans la masse lorsque la couleur de la pâte intérieure et de l’émail superficiel est similaire. Les carreaux émaillés non teintés dans la masse risquent davantage, en cas d'écaillage, de faire ressortir la différence de couleur entre la surface et le support sous-jacent.
Les carreaux non émaillés ne prévoient évidemment pas d'émail colorant et sont à leur tour divisés en deux types principaux selon la technique de production : il existe des carreaux non teintés dans la masse, où il n'y a pas de différence entre la surface et le support, de sorte que même en cas d'usure, la partie inférieure affleurante est pratiquement identique à la partie supérieure endommagée, mais la gamme des couleurs possibles est limitée à celle des argiles utilisées ; un autre type de carreaux est celui des carreaux non émaillés à double chargement, où la présence de deux distributeurs permet d'effectuer un premier versement, appelé chargement de poudre de couleur unie, et, après un premier pressage, un second chargement de matériau plus précieux qui enrichit et décore la surface.
Le produit étant le résultat d'un processus de cuisson industriel, les lots de carreaux produits peuvent présenter des différences de couleur par rapport à l'échantillon de référence : cette différence est définie comme un « ton » et les différentes productions sont divisées, emballées et identifiées en fonction de ce ton. Au moment de l'achat, assurez-vous de disposer d'un stock homogène de carreaux du même ton et prévoyez une quantité supplémentaire (les « chutes », dans une quantité égale à 10 % du total) pour les éventuelles ruptures et ajouts, car si vous achetez des carreaux à une date ultérieure, il n'est pas garanti que vous disposiez du même ton.
Pour la même raison, il est nécessaire de prêter attention au calibre, c'est-à-dire à la réduction dimensionnelle du carreau céramique par rapport à une valeur nominale. Dans la production industrielle de carreaux, il est impossible d'obtenir des produits de dimensions identiques. Dans la phase de sélection, les carreaux sont donc choisis et regroupés en lots de dimensions similaires, dans le respect des tolérances établies par les normes. Quant au ton, le calibre est par ailleurs indiqué sur l'emballage par un chiffre (le calibre va de 0 à 9).
CARACTÉRISTIQUES MÉCANIQUES SUPERFICIELLES
Les normes EN 101, ISO 10545-6 et ISO 10545-7 réglementent certaines caractéristiques des carreaux en ce qui concerne la résistance de la surface à l’abrasion et à l'usure.La dureté de la surface identifiée par l'échelle MOHS définit la capacité de la finition de la surface à résister aux rayures et aux éraflures.
Selon la norme EN 101, les carreaux sont classés de 1 à 10 en fonction de la résistance croissante des minéraux utilisés à l’abrasion.
L'échelle de dureté MOHS est la suivante :
- Talc
- Gypse
- Calcite
- Fluorite
- Apatite
- Feldspath
- Quartz
- Topaze
- Corindon
- Diamant
Le carreau présentant la plus grande dureté Mohs aura le moins de risque que d'autres matériaux puissent l'érafler ou le rayer de façon permanente.
Les tests effectués pour déterminer la résistance à l'abrasion sont essentiellement au nombre de deux et dépendent du type de surface :
- Résistance à l'abrasion profonde (carreaux non émaillés).
On mesure le volume enlevé dans des conditions particulières d'abrasion (abrasion profonde). On considère que le carreau est d'autant plus résistant que le volume de matière enlevée est faible.
- Résistance à l'abrasion superficielle PEI (carreaux émaillés).
Un processus d'abrasion superficielle est simulé par des cycles d'usure d'intensité croissante, et l'évaluation des effets qui en découlent est effectuée par un examen visuel dans des conditions d'observation spécifiques. En fonction du résultat de ces observations, une classe de résistance à l'abrasion est attribuée au carreau mesuré.
La résistance à l'abrasion superficielle (indice PEI) est la capacité de l'émail à résister à l'action de l'usure.
Selon la norme (ISO 10545-7), les carreaux sont classés en cinq catégories en fonction de leur utilisation prévue :
- PEI I: Produits destinés aux environnements soumis à un trafic léger et sans abrasions ; par exemple, les salles de bains et les chambres à coucher ;
- PEI II: Produits destinés aux environnements soumis à un trafic moyen et à une action abrasive moyenne à faible ; par exemple, les bureaux et les salons ;
- PEI III: Produits destinés aux environnements soumis à un trafic de moyen à lourd avec une action abrasive moyenne ; par exemple les entrées et les cuisines des maisons privées ;
- PEI IV: Produits destinés aux environnements soumis à un trafic intense, par exemple les magasins et les bureaux publics ;
- PEI V: Produits destinés aux zones soumises à un trafic particulièrement intense.
La glissance d'un sol est liée à la sécurité de la déambulation et constitue donc une exigence fondamentale pour obtenir l'habitabilité/accessibilité.
Le coefficient de glissance, indiqué par la valeur « R », (qui est liée à l'angle d'inclinaison auquel la personne perd l’adhérence au sol) classe les produits sur la base de leur coefficient de frottement, en fonction d'un environnement spécifique ou des exigences spécifiques de l'utilisation prévue, indiqués par un ordre croissant de dangerosité. La norme fait une distinction entre la glissance des surfaces praticables dans les zones où les gens marchent chaussés (R9-R13), et dans les zones où les gens marchent pieds nus (A, B, C).
On distingue les classes de glissance suivantes et les indications des domaines d'utilisation respectifs :
- R9: zones d'entrée et escaliers avec accès depuis l'extérieur ; restaurants et cantines ; magasins ; cabinets médicaux ; hôpitaux ; écoles.
- R10: salles de bains et douches communes ; petites cuisines dans les établissements de restauration ; garages et sous-sols.
- R11: zones de production alimentaire ; cuisines moyennes des établissements de restauration ; environnements de travail avec une forte présence d'eau et de boue ; ateliers ; blanchisseries ; hangars.
- R12: environnements destinés à la production de denrées alimentaires riches en graisses telles que : produits laitiers et dérivés ; huiles et charcuterie ; grandes cuisines des établissements de restauration ; départements industriels avec utilisation de substances glissantes ; parkings.
- R13: environnements avec de grandes quantités de graisses ; transformation des aliments.
Pour les environnements où l'eau est présente et où il faut marcher pieds nus, le sol doit répondre à des exigences encore plus restrictives. Ceux-ci sont classés dans les groupes d'évaluation A, B, C selon une valeur croissante :
- A: vestiaires ; zones d'accès pieds nus ; etc.
- B: douches ; bords de piscine ; etc.
- C: bords de piscine inclinés ; échelles immergées ; etc.
SURFACES et PROCÉDÉS
Les carreaux céramiques peuvent subir certains processus après le pressage et la cuisson qui contribuent à modifier leurs caractéristiques de surface et, dans certains cas, à définir l'usage auquel ils sont destinés.Le carreau structuré présente une surface en relief, donc rugueuse et opaque, ce qui le rend très similaire à la pierre naturelle et garantit une moindre glissance. Il s'agit donc d'un matériau particulièrement adapté aux pavages extérieurs.
Le semi-polissage et le polissage sont des processus essentiellement identiques où les meules abrasent la surface en enlevant de la matière : dans le premier cas, le travail est effectué sur un produit non émaillé et environ 1 mm de matière superficielle est enlevé, tandis que dans le second cas, le travail est effectué seulement après l'émaillage et seulement 2-3 dixièmes de mm sont enlevés.
Le polissage, également appelé lustrage, est un processus effectué en phase de production sur un carreau non émaillé, qui élimine une partie de la couche superficielle, et qui permet de rendre le carreau complètement brillant. Il est réalisé avec des têtes rotatives en diamant avec un grain très fin qui permet d'avoir une surface polie identique à un miroir, non hermétique à l'eau.
L'absorption dépend de la porosité initiale de la pâte du matériau à polir et rend le matériau sujet aux taches, il est donc conseillé d'effectuer un traitement anti-taches.
Le polissage est un processus mécanique effectué à l'aide de meules sur un carreau émaillé afin de rendre la surface du grès plus lisse et plus brillante.
Il existe différents types de polissage :
- superglossy : c'est-à-dire poli sur toute la surface.
- patiné : la surface du carreau reste irrégulière, veloutée au toucher, pas tout à fait brillante.
- en crête : seules les parties les plus saillantes de l'émail sont rodées de manière parfaitement brillante, les parties inférieures ne le sont pas (ex. « Accademia »).
Le carreau est imprimé numériquement avec le graphisme souhaité (effet marbre, bois, pierre, résine, ciment), émaillé avec un vermis sablé et rodé pour obtenir un effet brillant ou semi-brillant selon le type de polissage.
La rectification des bords des carreaux est un aspect important à considérer si des joints très fins sont nécessaires. Ce procédé permet de placer les carreaux très près les uns des autres, avec des joints presque imperceptibles et droits, pour obtenir un résultat raffiné, élégant et moderne.
La rectification est un procédé de post-production effectué avec des machines à découper où les bords sont coupés pour former des angles de 90°. Grâce à une opération d'abrasion mécanique, les dimensions du carreau sont réduites, ce qui permet d'obtenir un carreau aux bords parfaitement équarris et généralement d'un seul calibre. En plus de cette opération, il sera nécessaire de chanfreiner le bord visible pour le rendre moins tranchant.
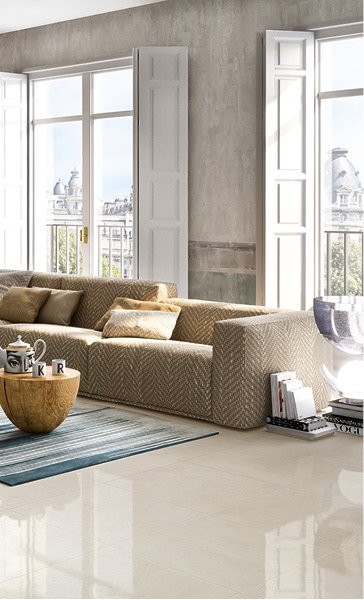
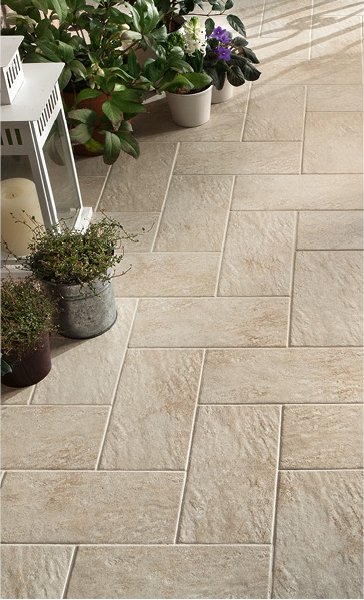
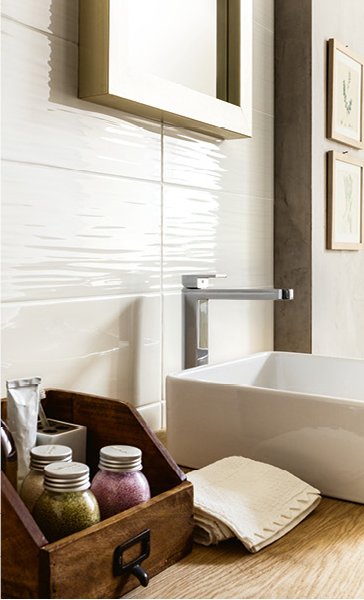